This is a description of how we at Johannas Stadsodlingar (urban farms) and Concinnity together have built Johanna’s aquaponic pilot facility. We want to share how we did it and our thinking behind it. There is quite a lot to think about, so there will be several posts to cover most things.
- Part 1 – start and prior knowledge
- Part 2 – design
- Part 3 – build log
- Part 4 – water quality and nutrients testing
- Part 5 – production management (this blog)
- Part 6 – distributed ledger/block chain integration (coming soon)
Cultivation Management Platform
The digital systems we have built are based around the vision we set out with at the start of the project. We call it the Cultivation Managment Platform.
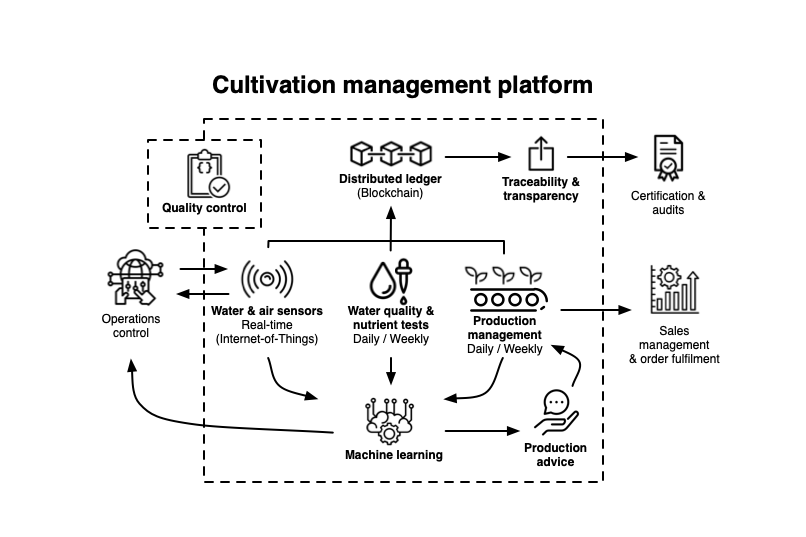
The CMP consists of four parts:
- Water quality and nutrients tests
- Water, air and automation sensors
- Production management
- Distributed ledger / block chain
In this part we will describe our work with the production management system.
Production management system – overview
With digital tracking, or production tracking, we collect data on how the cultivation itself is progressing. The main components of this system are a mobile app and a cloud-based service with which the app communicates. With the mobile app, we record every significant event during a plant’s path through the system, from seed to finished lettuce head! All data is stored in the cloud service and is accessible both from the app and from an administrative interface in the service.
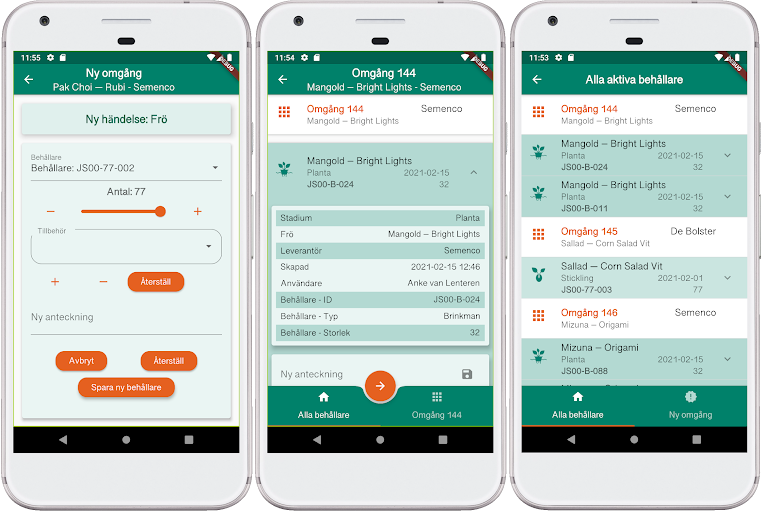
Cultivation process as data
The cultivation process is organized in what we call batches, where one batch is one or more germination occasions of the same seed made at the same time. As a plant goes from seed to harvest, we generate and record four events that we call Seed, Seedling, Plant and Harvest. Each batch in turn consists of one or more ”containers” where the plants grow. At the start of a batch, the seeds are placed in substrates in trays with between 77 and 150 plants. These trays stand on a cultivation table, a shallow basin with a few centimeters of water. The tray is covered with a plastic hood for higher temperature and humidity. The first event, Seed, is recorded when we sow a tray.

Anke moving seedlings from a tray to a raft
The germination period is about a week long, after which the tray is moved to another cultivation table where the seedlings can continue their growth for a few weeks. When this move is made, we register a Seedling event. How long the plants spend as seedlings depends on the type of plant.
When the seedlings have grown to the right size on the tray, it is time to move them out to the large cultivation basins. This is done by moving each individual plant to a raft. The rafts are just under a square meter in size, and hold 30 or 32 plants. The two different types of rafts have different sized holes where the plant is placed and are therefore suitable for different types of plants. For each raft, we register a Plant event. After a number of weeks on the rafts, again for different lengths of time depending on the type of plant, the finished plants are harvested. This is usually done the same day or the day before they are delivered to the customer. For each raft that is harvested, we create a Harvest event.
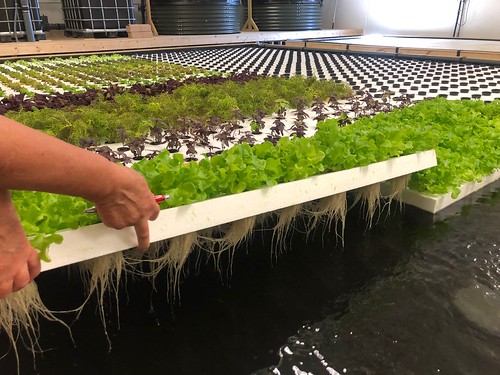
A raft is being brought out for harvest
For each event, we record the time of the event, who does the registration, and the number of plants that are currently on the tray or raft. For example, some seeds have not germinated properly and we register the loss when we create the Seedling event. In the case of Seed and Plant events, we register the ID of the cultivation tray or raft used. You can also add a free text note. In addition, the following data is stored for the various events:
- Seed: seed variety and supplier, ID of cultivation tray, number of seeds and any cultivation accessories used
- Seedling: the number of seedlings
- Plant: raft ID and the number of plants
- Harvest: the number of plants harvested
Implementation
The production management system consists of two main parts; a mobile app and a server with which the app communicates via HTTP and where we store the data registered via the app. The app is built with the Flutter framework. Flutter makes it possible to create apps that use the same source code but can run on both Android and iOS-based phones and tablets. The cloud service is built with the Django framework, a framework for all types of HTTP-based backend solutions. In addition to Django, we also use PostgreSQL as a database and Hasura which provides a GraphQL API to the database.
In the next post we will have a look at our distributed ledger/block chain integration.
The text in this posted is licensed under Creative Commons BY-NC-SA International.